Most real estate professionals by now know the Matterport camera as the leading name in 3D “reality capture.” Using a combination of infrared emitters, sensors, and high definition cameras, the Matterport quickly and efficiently captures… well… everything it sees. 3D models like these that are high quality and easy to interact with are the gold standard for real estate sales, especially now in the age of coronavirus when remote viewing is everything. In addition to stunning visual imagery captured by the Matterport camera, an often overlooked capability is waiting just beneath the surface.
Millions of data points
Sure the Matterport camera captures high dynamic range spherical 3D photo panoramas at 138 megapixels each. But that’s really only one third of what the device does. In order to position each one of the 3D scans in space and align the overall model, the Matterport uses an ingenious system of infrared emitters and receivers to project an invisible (to the human eye) grid on all the surfaces it scans. Imagine a grid like the holodeck on Star Trek: The Next Generation. As each scan is placed in space, it logs millions of points of positioning data. Most people never see that data and have no reason to, but it’s all there, right under the surface.
One of the many texture files generated by the Matterport scans. Along with the .xyz plot data, these are used to help build the 3D model of the scanned space.
All that data can be extracted from a Matterport scan, but it still needs to be converted to a more usable format. That’s where CAD tracing comes in. We are able to trace the raw data from any scan and produce portable, editable 3D models suitable for working with Autodesk Revit and other design programs.
CASE STUDY: 3-Family home under construction in Boston, MA
This client was a builder in the process of rehabilitating a 3 story townhouse we started with scanning this project just prior to drywall installation to preserve a photographic record of everything behind the walls. We were able to capture the entire building within about 90 minutes while the crew worked outside. The next day, the 3D model was available and the builder now has a high quality permanent photo record of the plumbing, electrical, and framing on his project. The underlying data was then traced by our team to create a detailed CAD model and associated shop drawings.
The original scan:
Deliverables from Enhanced CAD work:
Detailed shop drawings of current build status can be rendered quickly and accurately. Available in most CAD formats, exported to pdf.
Autodesk Revit model - shown here in partially exploded view. Click here to explore the actual Revit Model
In addition to the enhanced portable models and drawings of the building, the project deliverable also included a full still photo survey of the property:
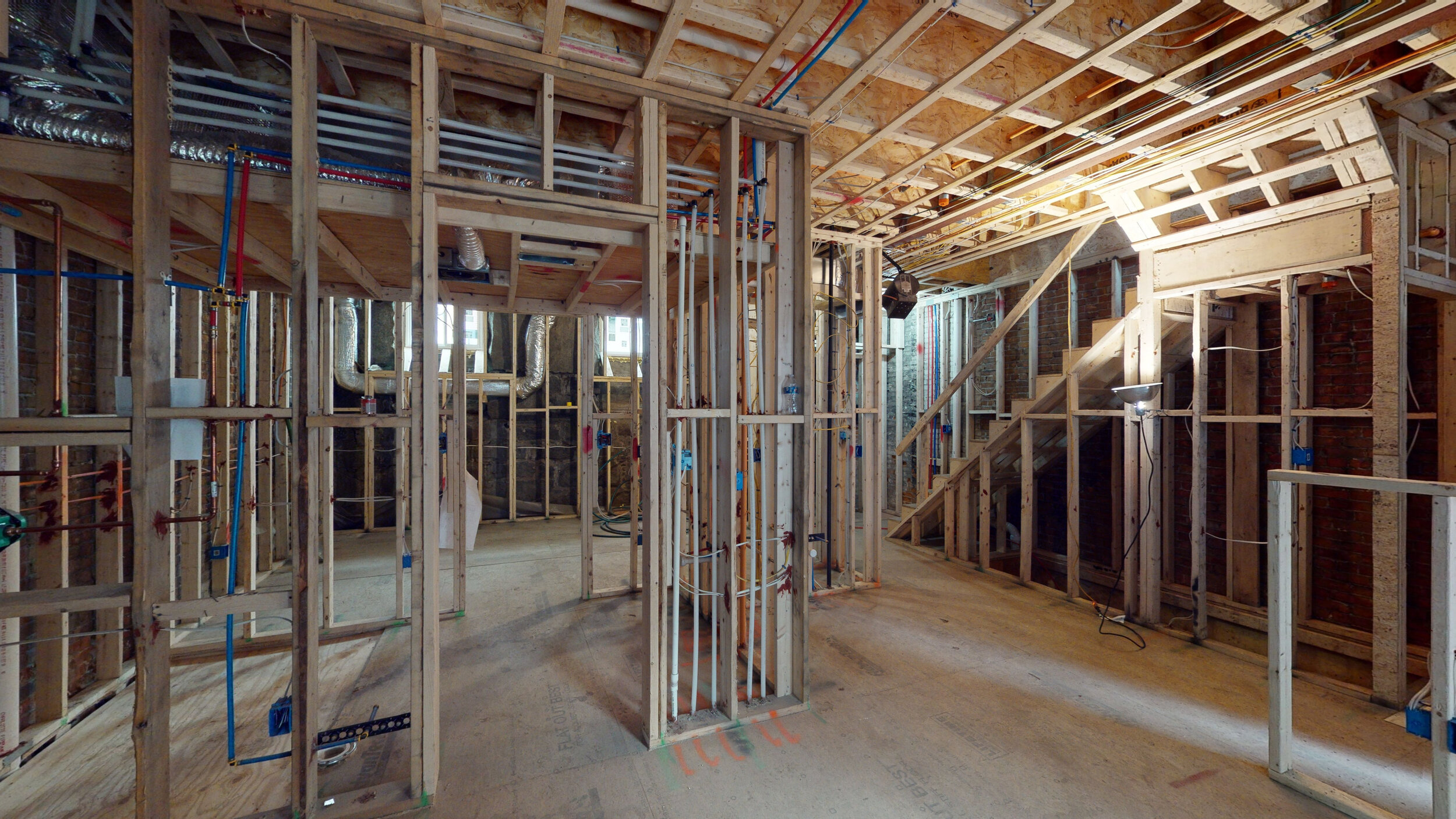
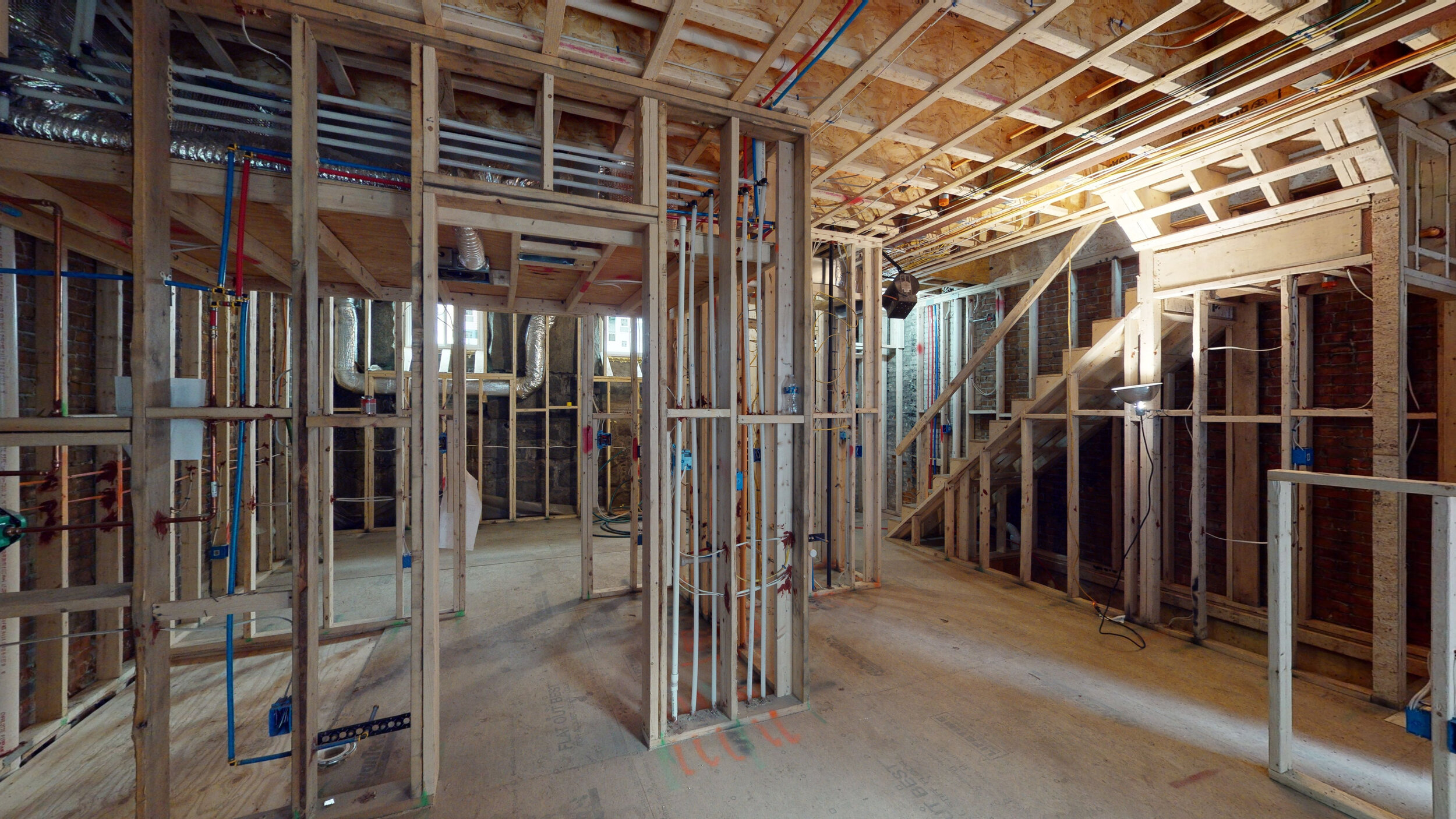
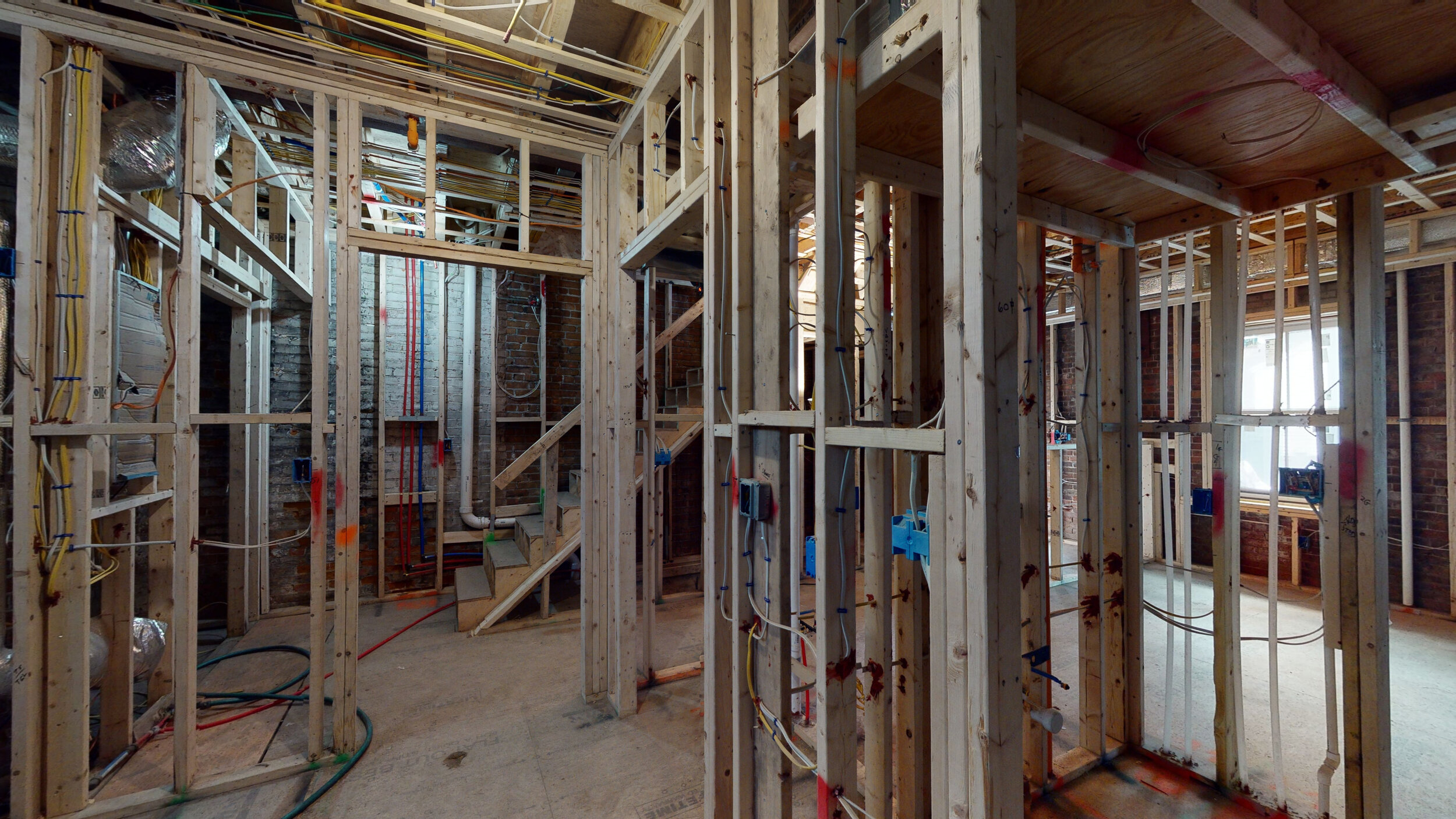
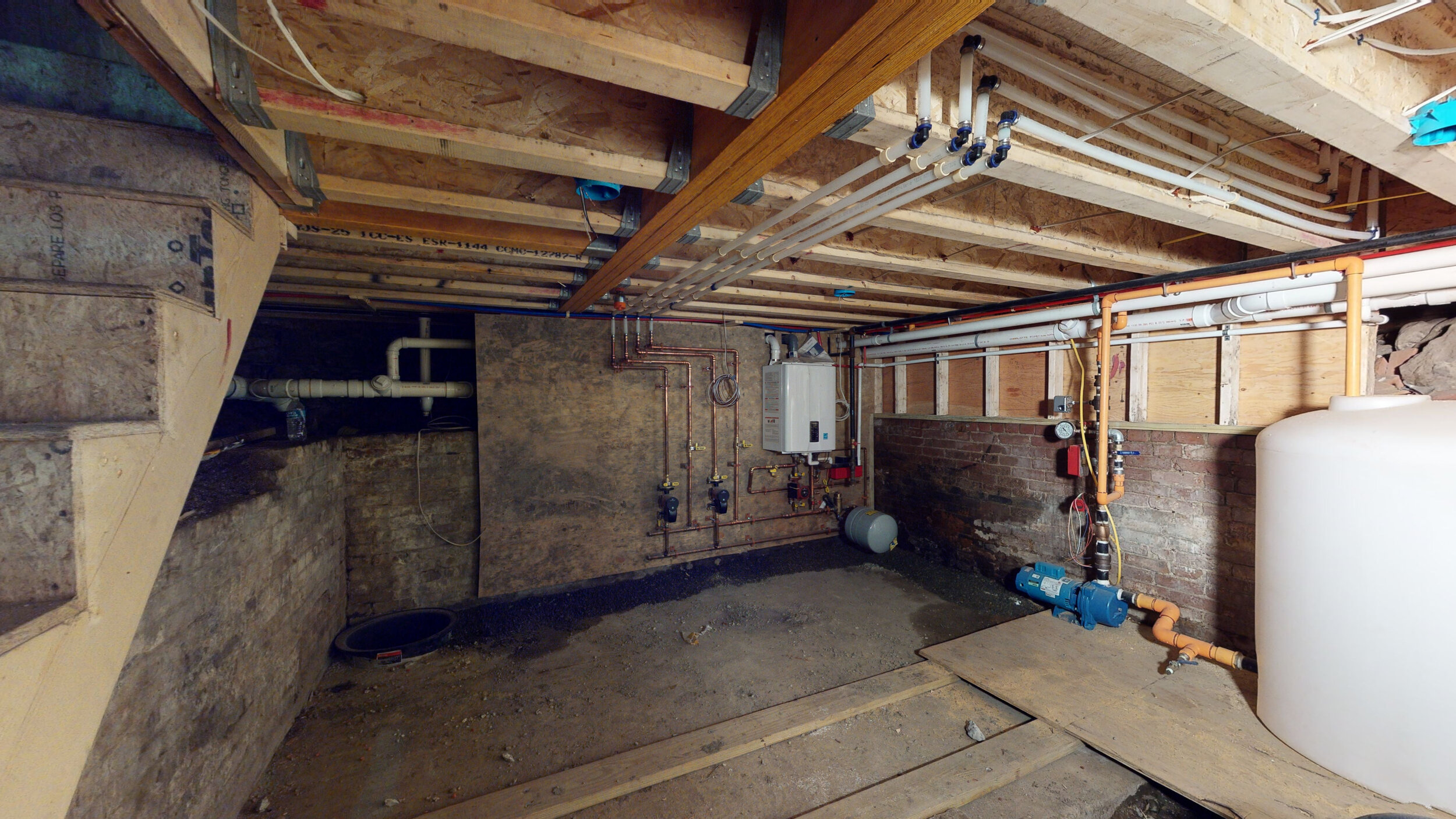
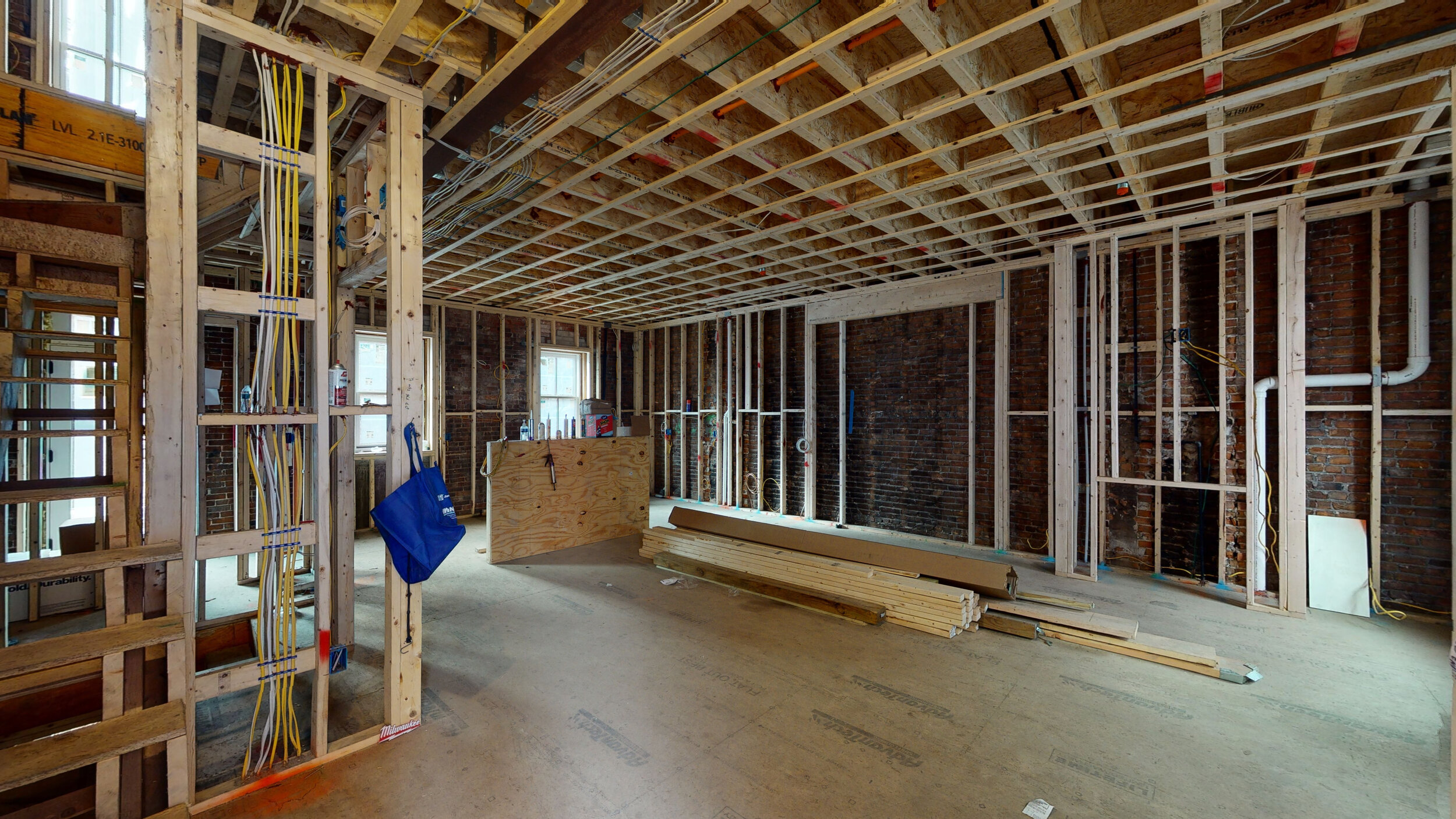
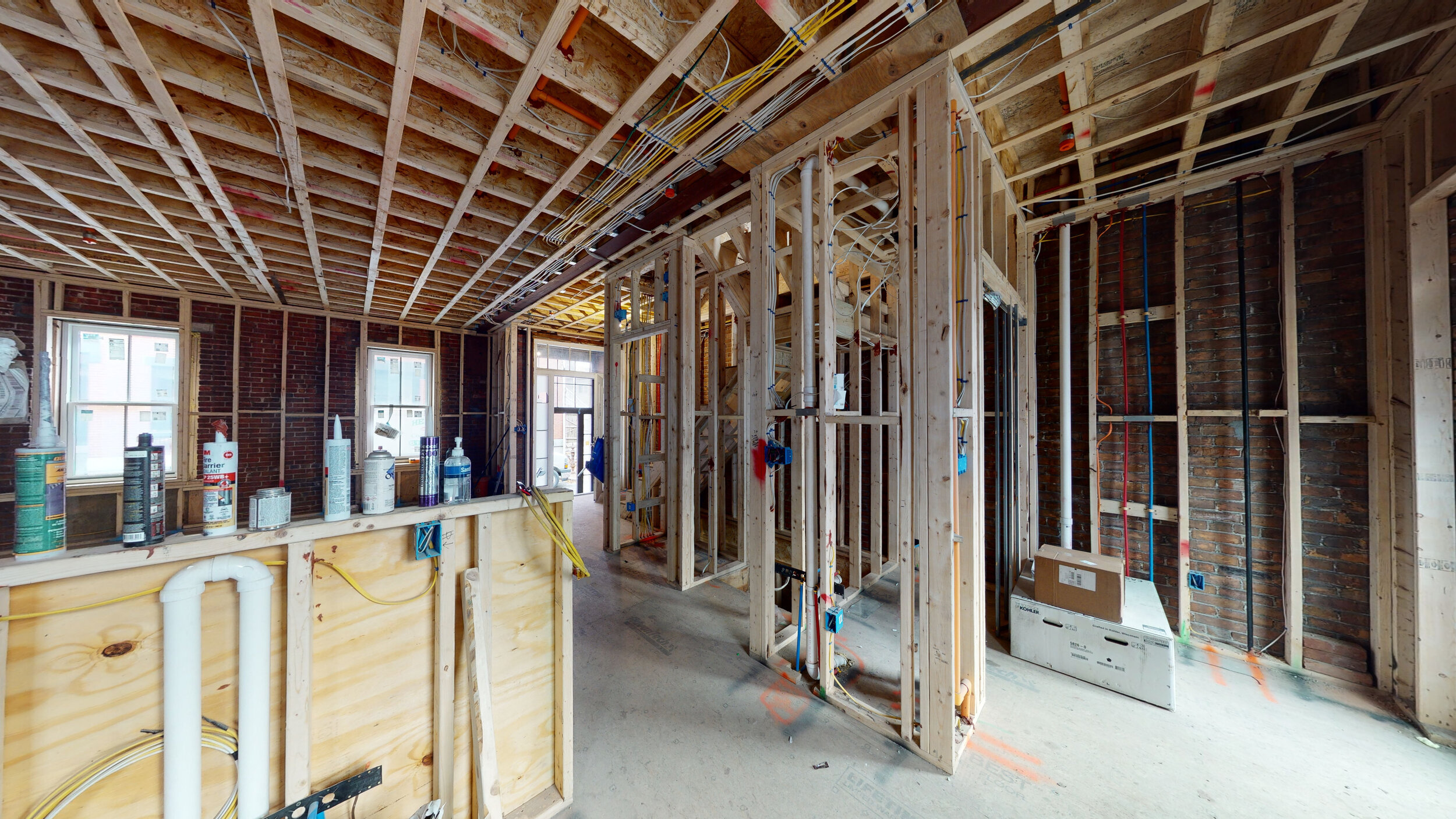
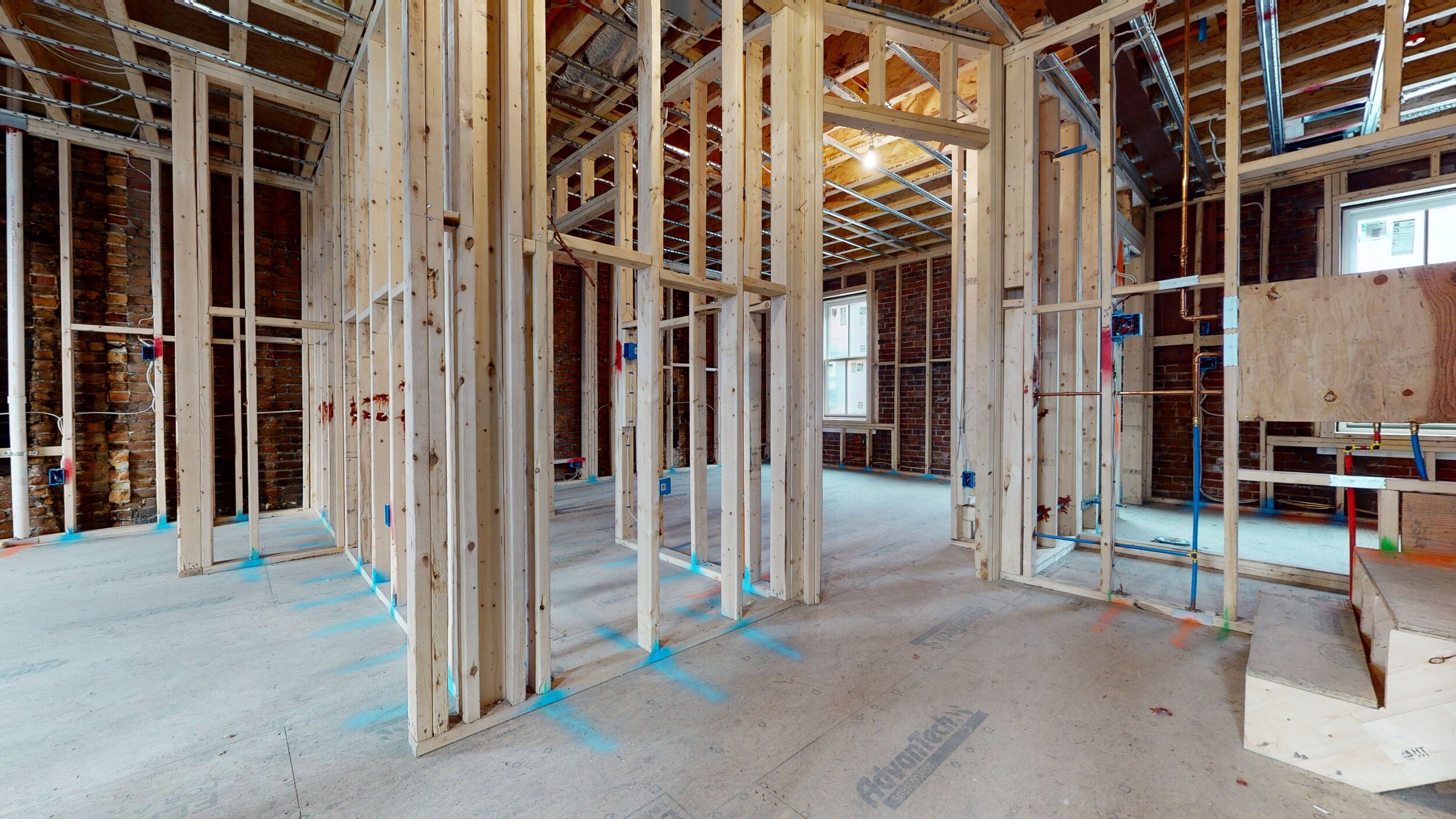
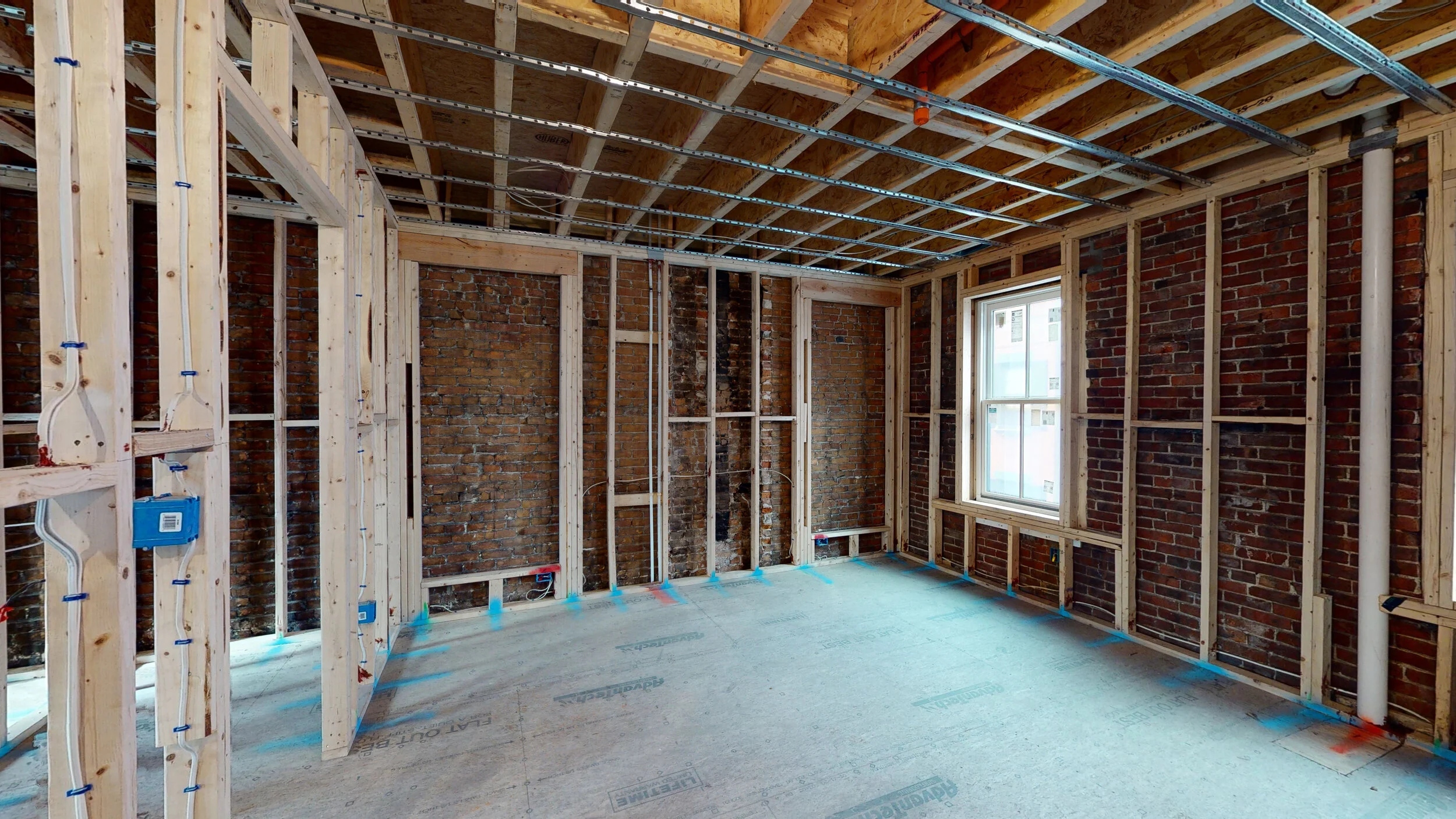
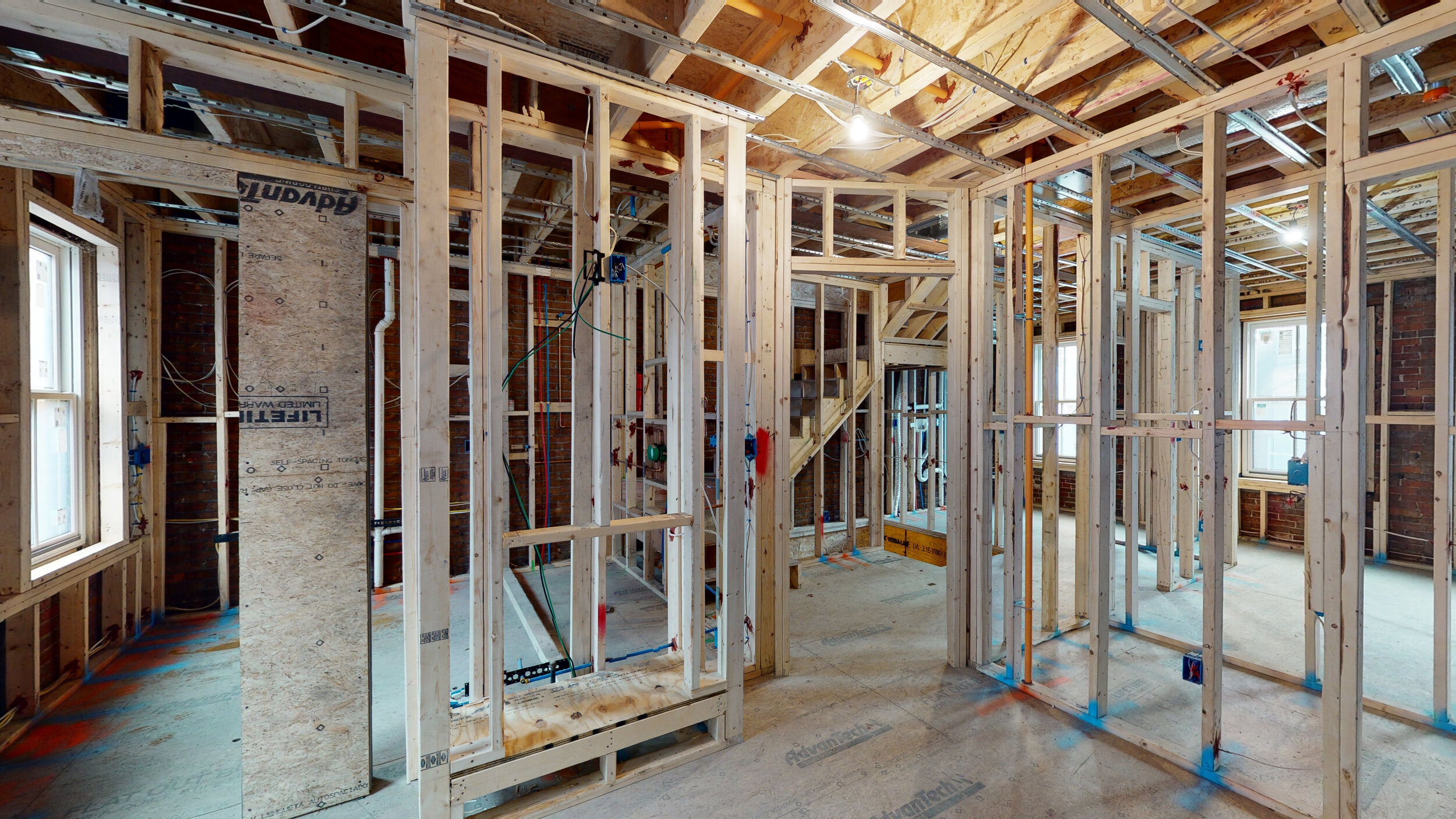
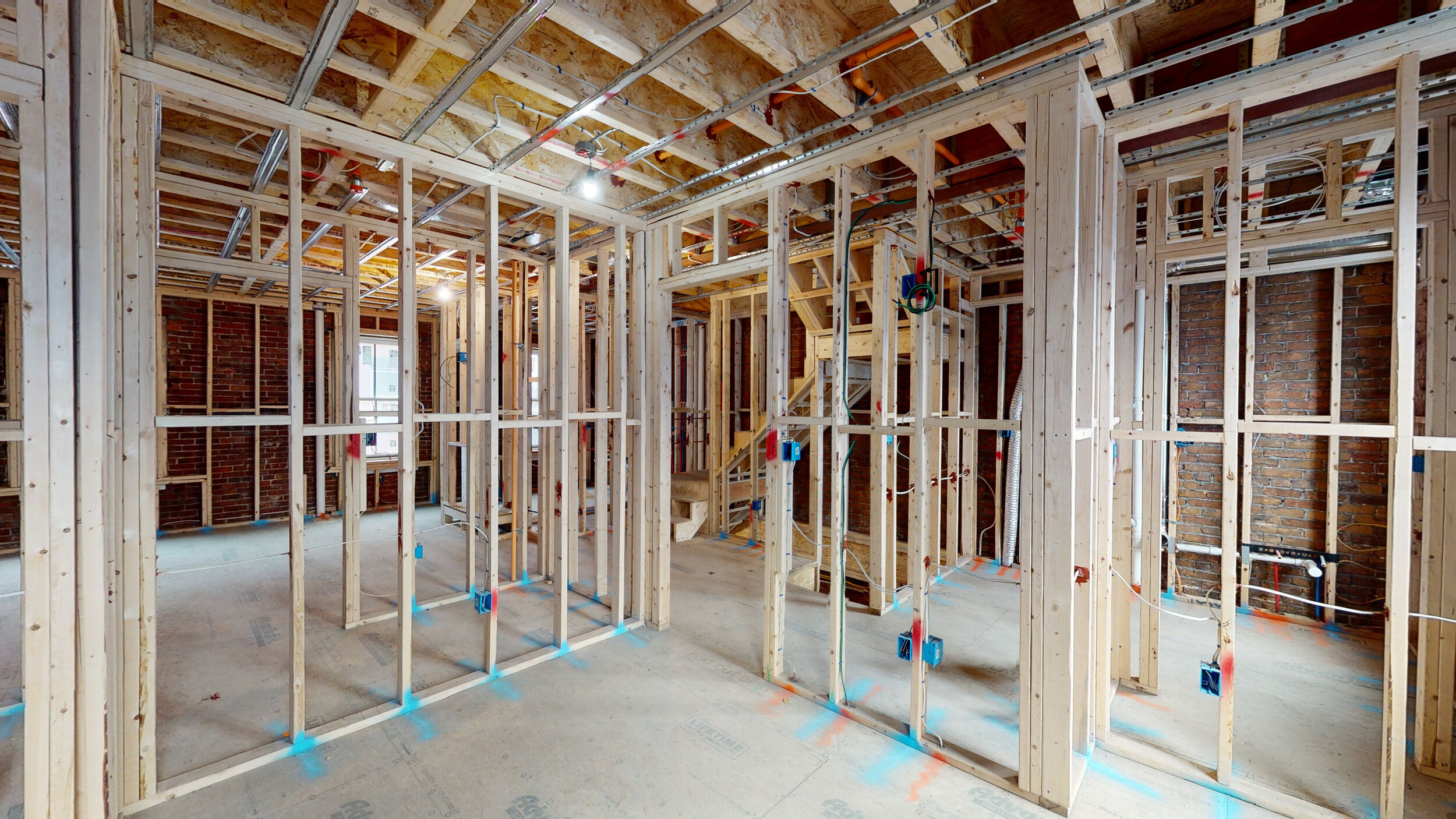
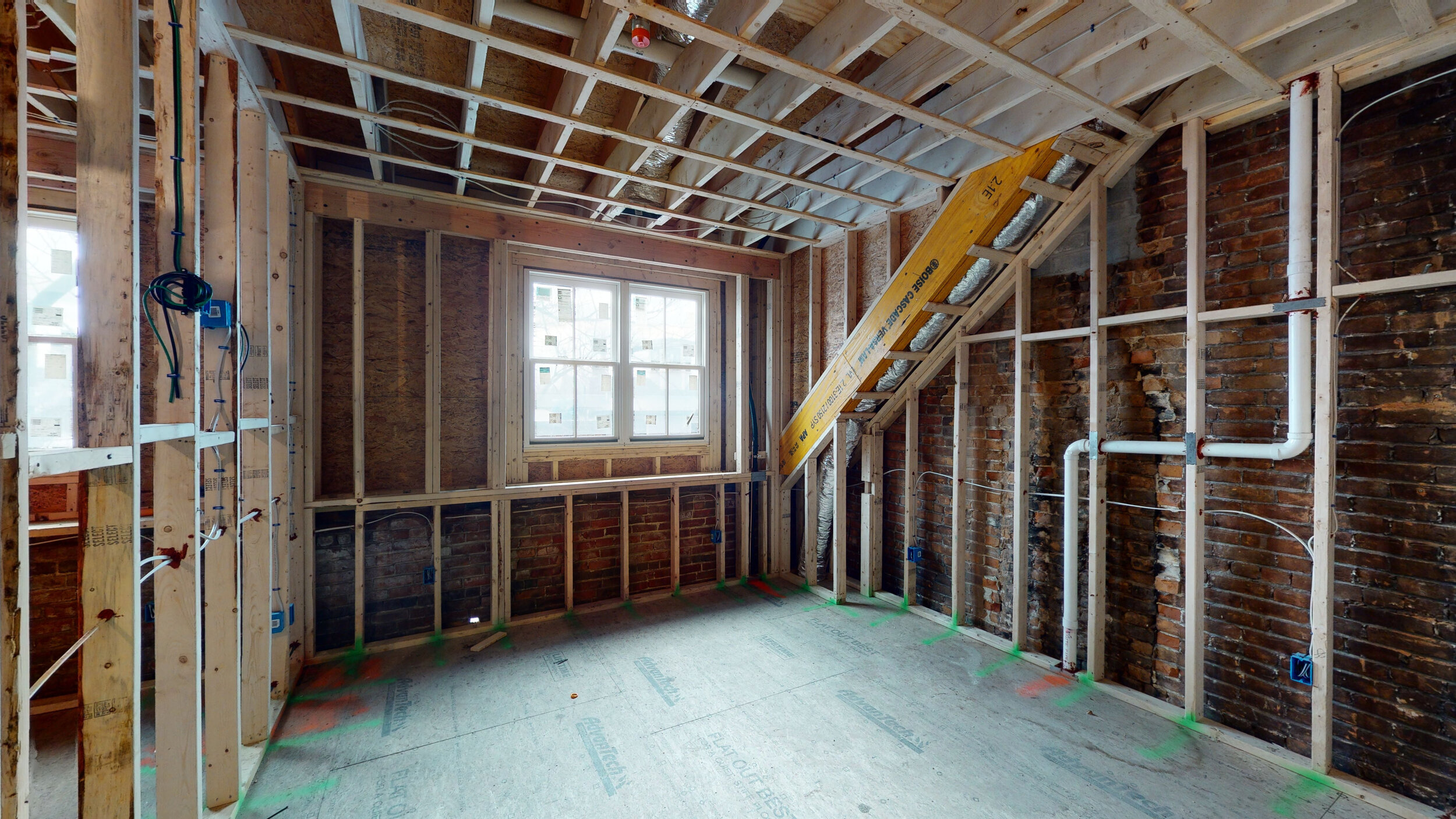
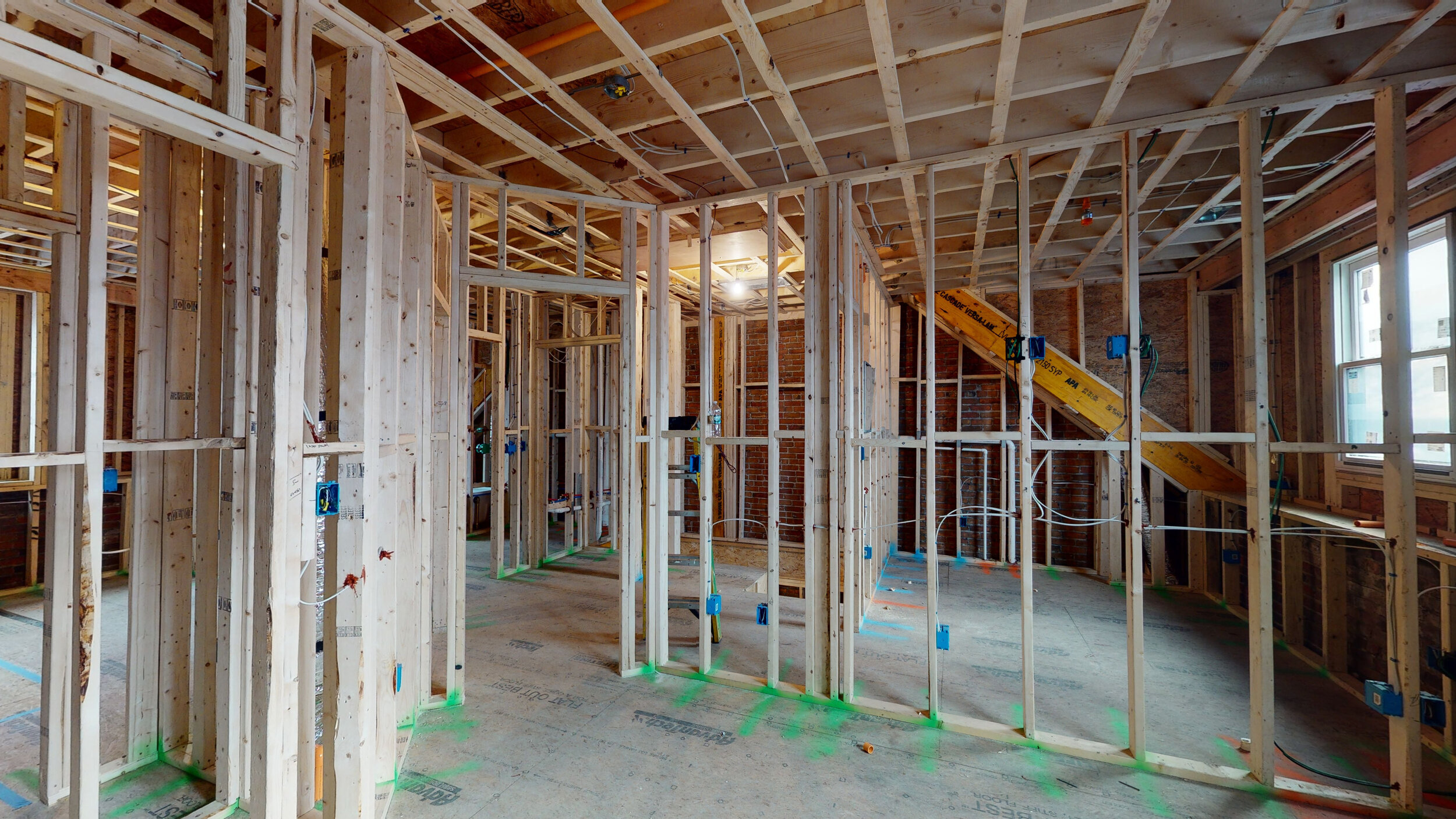
The photo survey does not end at the walls either: every floor and ceiling is captured and rendered as a flat 2D photo for easy interpretation:
Reality capture, enhanced
While the Matterport camera remains the premier device for top of the line photo reality capture, we’re taking it a step further. Accessing all the raw data that lies under the surface of the scans, we can now massively accelerate the process of collecting measurements for as built drawings, creating large savings in time and project costs. Any space scanned by JS O’Connor Photography is now eligible for enhanced CAD tracing
Coming soon:
Case study #2: Extracting MEP (Mechanical, Engineering & Plumbing) Data for BIM Modeling of a Large Mechanical Room